Producing Banana Fiber and Paper from Waste
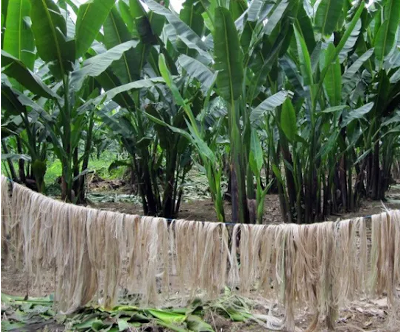
Problem
Plastics and paper are the binding forces that help our information age to proceed further and conquer new frontiers. However, both these essential goods are sourced from non-renewable sources such as petroleum and forest trees. There is an urgent need to find alternatives to plastic polymers since they are non-biodegradable as well, which persist in the environment for ages. Paper consumption was expected to go down steadily with the onset of the electronic age, but it is nowhere near reduction. Further, the conventional method of making paper is highly polluting, which uses numerous chemicals for treating the wood fibres to form pulp, and in the process of getting papers of acceptable properties.
Traditional Solution

On the other hand, the agricultural sector in India produces a vast range of natural fibers that can be utilized to produce both fiber and paper. Natural fibers can be defined as substances that are obtained from plants such as agave, banana, jute, cotton, etc. which can be spun into filaments, threads or ropes and can be woven. Among these, banana fiber has emerged as a new eco-friendly innovation since it is produced from banana stem, which is a waste material after harvesting the banana fruit.

Typically in banana cultivation, the stems of the plants are chopped off and thrown away once the fruits are sold. These wasted stems typically lay around in the farm and clearing from the land would cost a farmer almost about Rs. 3000 on average. Now, however, a new technology plant has managed to manufacture eco-friendly banana paper out of these banana stems!
The knowledge of extracting fiber and paper from banana was well known since the 13th Century when Japanese processed it. However, it was a time-consuming and costly process where banana stems were first boiled in lye to soften them and then prepared from shredding to extract yarn. They produced banana fibers of varying degrees of softness, yielding yarns and textiles with differing qualities for specific uses. The fibers extracted from the outermost stem layers are the coarsest, which are suitable for mats, bags and tablecloths, while the softest innermost fibers are used for the traditional Japanese handloom cloth-making process.
Innovative Solution
In 2000s, Eco Green Unit a paper manufacturing firm attached to the Agri Business Directorate of the Tamilnadu Agricultural University, and Chaitanya Mandal a Pune-based NGO innovated a new process to extract fiber from banana stems. They created a simple mechanical process where a machine can extract fiber in an efficient manner. This banana fiber extracting machine can be easily operated by an unskilled workers and gives maximum output of fibers. These eco-friendly fibers have suitable properties like low density, appropriate stiffness, high disposability and renewability.
Process
The outer sheath from the banana stem is first peeled off, the inner layers are flattened and fibers are stripped off either manually or through machines. Heaps of banana stems are piled up near at the processing unit and workers begin slicing the banana stems into thin strands. These sliced stem pieces are then passed through the machine on the fixed platform that separates the gummy lignin and water content from it. The shredded fiber is then cleaned and dried in the sun before being bundled into yarn that makes notepads, stationery items, lampshades, and handicraft.
Eco Green Unit has developed this machinery by using German technology, which uses 1HP single phase motor to power it. The machines can be easily operated by semi-skilled women, has less maintenance, and safe to operate. Around 5-6 stems are needed to extract 1kg of fiber, depending upon their quality and the water content in them.
Production
India leads the world in terms of banana production, producing around 18% of the worldwide crop of 139 million metric tons (2012). Maharashtra and Tamil Nadu are the leading banana producing states. Although about 500,000 hectares are under banana cultivation, only 10% of the banana stem waste is processed into fiber. If farmers decide to supply banana stems to these fiber processing units, they would not only clear waste without any cost, but also would benefit from their earnings. They can set up a small-scale unit at a cost of INR110,000, that would employ a few semi-skilled workers. The quality of banana stems cultivated in Maharashtra is found to be ideal for fiber extraction. They are of superior quality and have more brightness and shine when compared to the fibers from Tamil Nadu and Gujarat.
[post_grid id=’43’]